How to Manufacture High-Quality Wicker Plastic Chair Molds: Expertise by ISM Molds
In the competitive world of furniture manufacturing, wicker-style plastic chairs have gained immense popularity for their lightweight durability, aesthetic appeal, and versatility. At the heart of producing these chairs lies a critical component: the plastic chair mold. As a leading plastic chair mold manufacturer, ISM combines advanced engineering, material innovation, and decades of expertise to deliver molds that ensure precision, efficiency, and longevity. This article explores the key steps to creating superior wicker plastic chair molds and highlights how ISM stands out in the industry.
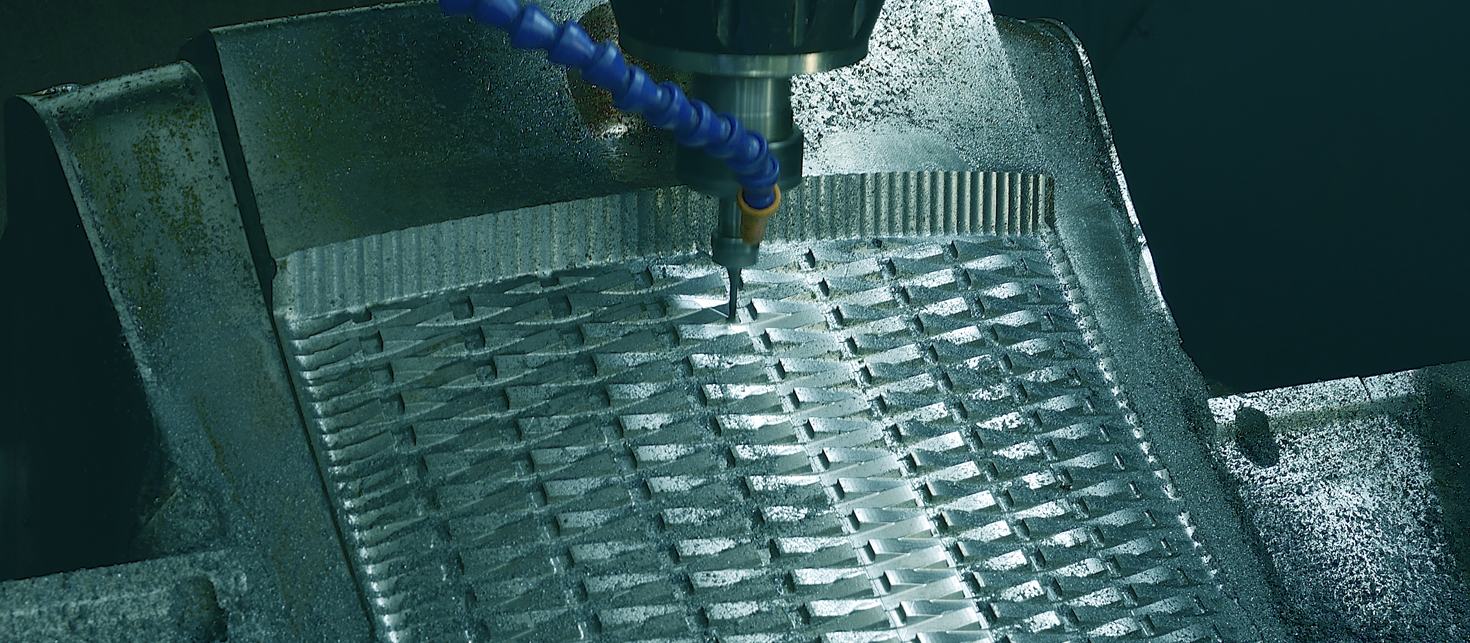
Key Steps to Manufacturing Premium Wicker Plastic Chair Molds
1. Design & Simulation
The foundation of a high-quality mold begins with meticulous design.
3D Modeling: ISM’s engineers use CAD/CAM software to create detailed 3D models of the chair, incorporating intricate wicker patterns and ergonomic contours.
Structural Analysis: Finite Element Analysis (FEA) simulates stress distribution, ensuring the mold withstands high-pressure injection cycles.
Material Flow Optimization: Moldflow simulations predict resin behavior to prevent defects like air traps or uneven cooling.
2. Material Selection
Choosing the right materials is crucial for durability and performance.
Mold Steel: ISM uses premium-grade steels (e.g., P20, H13) hardened to resist wear and corrosion, even under high-temperature cycles.
Resin Compatibility: Molds are tailored for specific plastics (PP, PE, or recycled materials) to ensure smooth demolding and surface finish.
3. Precision Machining
Advanced manufacturing technologies guarantee accuracy.
CNC Machining: High-speed CNC mills carve complex wicker textures and fine details into the mold cavities.
EDM (Electrical Discharge Machining): Used for ultra-precise detailing on hard-to-reach areas of the wicker design.
4. Cooling System Engineering
Efficient cooling is vital for cycle time reduction and product consistency.
Conformal Cooling Channels: ISM integrates 3D-printed conformal cooling lines that follow the mold’s contours, ensuring uniform temperature distribution.
Baffles and Bubbler Systems: These components enhance heat exchange in thick sections of the chair design.
5. Surface Finishing & Texturing
Achieving the authentic wicker look requires specialized finishing.
Chemical Etching: Creates realistic woven textures on the mold surface.
Polishing: Mirror-finish polishing ensures smooth demolding and reduces part defects.
6. Testing & Optimization
Rigorous testing ensures flawless performance.
Trial Runs: Initial injections identify issues like warping or sink marks.
Adjustments: ISM fine-tunes gate locations, cooling rates, and ejection mechanisms for optimal results.
Product Name | Morden style moulds office moulded foam shell eames rattan soffa baby manual mould chair |
Core & Cavity Steel | 2316# steel, S136, H13,718,SKD61,P20,S50C,45#steel,4Cr13, 3Cr13, Becu or based on customer's requirement |
Mould base & Standard Component | P20, 4cr13, h13.718 |
Steel hardness | HRC30-35 for base material; HRC45-48 for core and cavity material; HRC60-62 for special parts material |
Plastic material | PP,PC,PA,PA6,ABS,PET,PVC,POM,etc |
Cavity Number | 1*4 1*6 1*8 1*2 etc |
Injection System | Pin gate, Submarine gate, Valve gate etc. |
Cycle Time | Based on design |
Tooling lead time | 30-60 days |
Mould life | At least 1.5 million shots |
Transportation | By air or by sea |
Why ISM Molds Excels in Wicker Plastic Chair Mold Manufacturing
As a trusted plastic chair mold factory, ISM differentiates itself through:
Customization Expertise
From classic wicker patterns to modern designs, ISM crafts molds tailored to your brand’s unique aesthetic and functional requirements.Sustainability-Driven Solutions
We design molds compatible with recycled plastics, supporting eco-friendly production without compromising quality.Fast Turnaround Time
Leveraging automated machining and streamlined workflows, ISM delivers molds 20-30% faster than industry averages.Global Compliance
Molds adhere to international standards (ISO 9001, ASTM) and are compatible with all major injection molding machines.Lifetime Support
ISM provides maintenance, repair, and refurbishment services to extend mold lifespan and ROI.
Applications of ISM’s Wicker Plastic Chair Molds
Our molds are trusted for producing chairs used in:
Hospitality: Durable outdoor seating for hotels and restaurants.
Residential: Lightweight, weather-resistant patio furniture.
Commercial: Stackable chairs for events and offices.
Partner with ISM for Unmatched Mold Quality
Creating a superior wicker plastic chair mold demands technical precision, innovation, and deep industry knowledge. At ISM, we blend these elements to deliver molds that empower your production line with speed, consistency, and scalability.Whether you’re launching a new furniture line or optimizing existing processes, ISM’s expertise ensures your chairs stand out in design and performance. Contact us today to discuss your project and discover how we can elevate your manufacturing success!
Leave a Reply
Your email address and tel will not be published. Required fields are marked