Plastic Pallet Injection Mould Manufacturing: Precision, Durability, and Efficiency
In the fast-paced logistics, warehousing, and manufacturing industries, plastic pallets have become indispensable for their strength, hygiene, and reusability. Central to producing these pallets is the plastic pallet injection mould—a component that demands engineering excellence to ensure consistent quality and high-volume output. As a specialized plastic pallet mould manufacturer, ISM leverages cutting-edge technology and industry expertise to deliver molds that meet global standards. This article delves into the critical aspects of designing and manufacturing superior plastic pallet molds and highlights how ISM empowers businesses to optimize their supply chains.
Key Elements of High-Performance Plastic Pallet Injection Moulds
1. Advanced Design & Engineering
The foundation of a reliable plastic pallet mold lies in intelligent design.
Load-Bearing Analysis: Using CAD and FEA (Finite Element Analysis), ISM engineers optimize rib structures and wall thickness to ensure pallets withstand dynamic loads up to 5,000+ lbs.
Modular Design: Customizable mold configurations allow for multi-cavity production, interchangeable inserts, and compatibility with various pallet sizes (e.g., 48”x40”, Euro pallets).
Material Flow Simulation: Moldflow analysis prevents defects like warping or sink marks, critical for maintaining pallet flatness and stacking stability.
2. Robust Material Selection
Durability is non-negotiable for molds producing heavy-duty pallets.
High-Grade Steel: ISM uses hardened steels like 718H or NAK80, resistant to abrasion and corrosion from high-temperature polymers (e.g., HDPE, PP).
Reinforced Components: Core pins and ejector systems are engineered to endure repetitive stress cycles in 24/7 production environments.
3. Efficient Cooling Systems
Reducing cycle times while ensuring dimensional accuracy is paramount.
Conformal Cooling Channels: 3D-printed cooling lines follow the mold’s geometry, slashing cycle times by 25–30% and minimizing thermal deformation.
Baffles and Bubbler Systems: Target cooling in thick sections (e.g., pallet feet) to accelerate solidification.
4. Surface Finishing & Texture
Non-Slip Surfaces: Textured mold cavities create anti-slip patterns on pallet decks, enhancing safety in wet or oily environments.
Smooth Ejection: Precision polishing ensures clean demolding, reducing part rejection rates.
5. Testing & Validation
Prototype Trials: Initial shots verify load capacity, dimensional accuracy, and compatibility with automated handling systems.
Durability Testing: Molds undergo stress tests simulating 100,000+ injection cycles to guarantee longevity.
Why Partner with ISM for Plastic Pallet Moulds?
As a leading plastic pallet injection mould factory, ISM stands out through:
Customization Expertise
Tailor-made designs for nestable, rackable, or stackable pallets, including RFID/anti-static features.
Solutions for lightweight, heavy-duty, or hybrid pallet designs.
Sustainability Focus
Molds optimized for recycled plastics (rHDPE, rPP) to support circular economy goals.
Energy-efficient cooling systems reduce carbon footprint.
High-Volume Production Capability
Multi-cavity molds with hot runner systems enable mass production (1,000+ pallets/day).
Global Compliance
Molds meet ISO 6780, FDA (for food-grade applications), and EUR/EPAL standards.
End-to-End Support
From design consultation to mold maintenance, ISM ensures seamless integration with your production line.
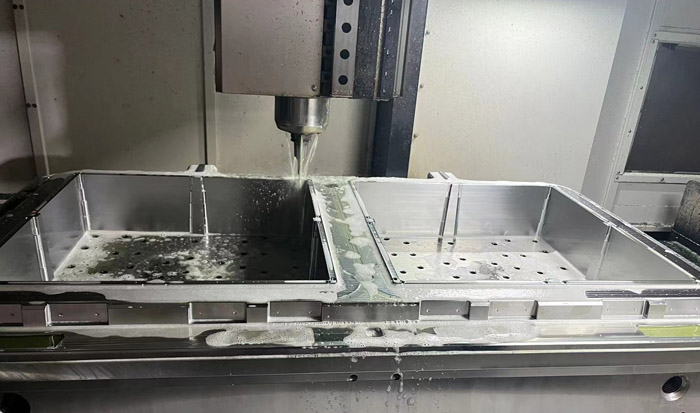
Applications of ISM’s Plastic Pallet Moulds
Our molds produce pallets trusted in industries such as:
Logistics & Warehousing: Durable pallets for forklift handling and automated storage systems.
Food & Pharma: Hygienic, washable pallets compliant with FDA and EU regulations.
Retail & Export: Lightweight, nestable pallets to minimize shipping costs.
Automotive: Anti-static pallets for sensitive component transport.
Leave a Reply
Your email address and tel will not be published. Required fields are marked