Plastic Crate Mould Manufacturing
1. Introduction
Plastic crate moulds are precision tools for mass-producing durable storage containers used in logistics, agriculture, and retail. This article details the design, manufacturing, and technological innovations behind these critical industrial assets.
2. Design Engineering
Key Design Elements:
Parting Line Strategy: Optimized for crate geometry (e.g., stacking ribs, handholds) to minimize flash and ejection stress.
Gate Systems:
Hot Runner Systems: Preferred for high-volume production (e.g., 8-32 cavities), reducing cycle time by 15% and material waste.
Cold Runner Systems: Cost-effective for prototypes or small batches.
Ejection Mechanism: Stripper plates + ejector pins ensure distortion-free demolding of deep-walled crates.
Cooling Channels: Conformal cooling designs maintain ±2°C uniformity, cutting cycle time by 20%.
Software Tools:
CAD (UG NX, SolidWorks) for 3D modeling
Moldflow® simulation for warpage/packing analysis
3. Material Selection
Component | Material | Hardness | Purpose |
---|---|---|---|
Core/Cavity | P20/718 Steel | HRC 30-35 | Balance machinability & durability |
High-wear inserts | H13/SKD61 | HRC 48-52 | Resists abrasive polymers (e.g., GF-PP) |
Base plates | S50C/1045 Carbon Steel | HRC 28-32 | Structural support |
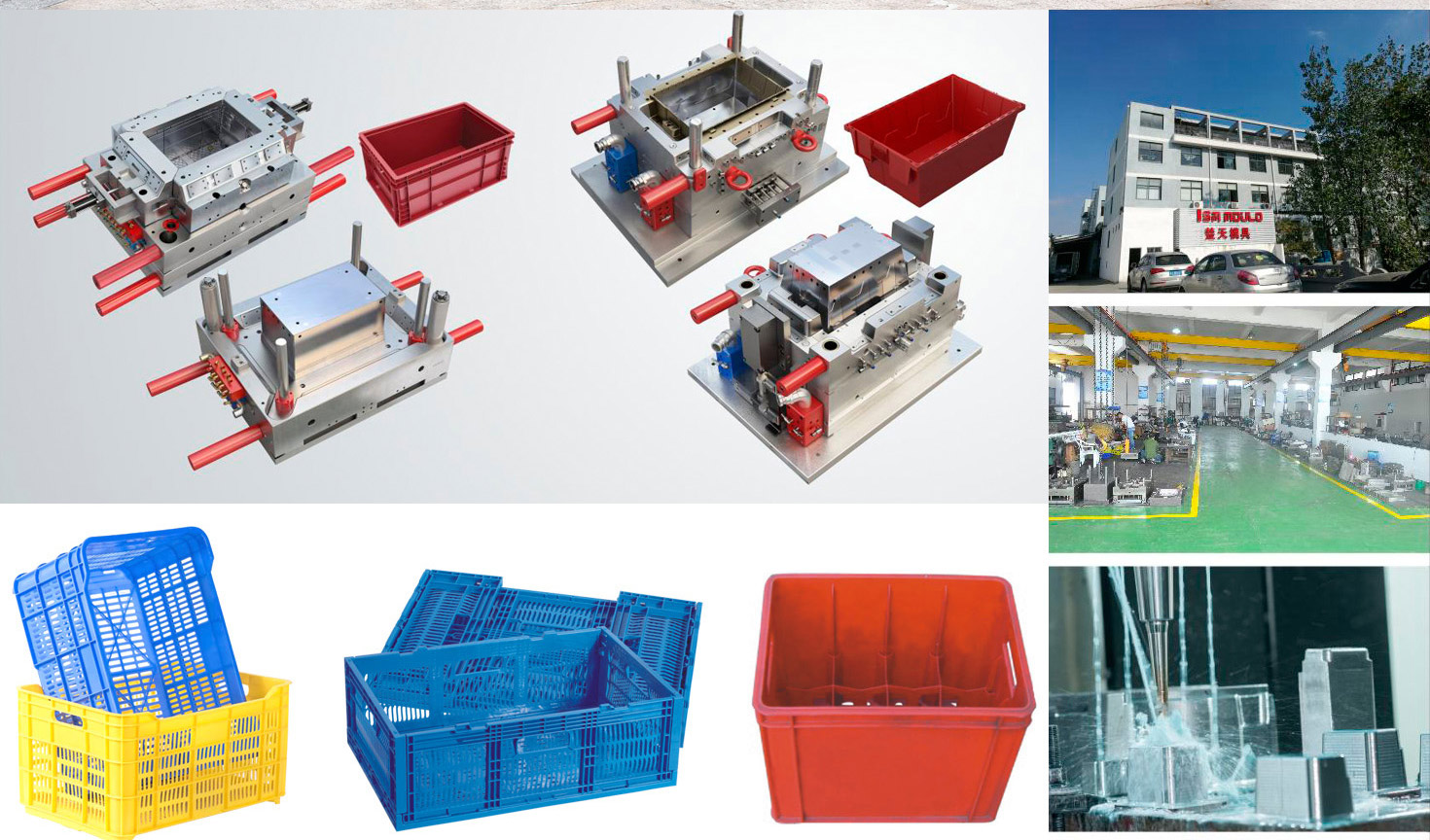
4. Manufacturing Process
Step-by-Step Production:
CNC Machining:
Roughing: ±0.1mm tolerance
Finishing: ≤0.03mm surface accuracy
EDM (Electrical Discharge Machining):
Creates complex geometries (e.g., textured surfaces, undercuts)
Heat Treatment:
Vacuum hardening (up to HRC 52)
Nitriding for corrosion resistance
Surface Enhancement:
Polishing: SPI-A1 (mirror finish for food-grade crates)
Teflon/DLC coating to reduce sticking
Assembly & Alignment:
Guided ejector systems with ≤0.01mm runout
Integrated sensors for real-time pressure/temp monitoring
5. Validation & Testing
Trial Phases:
Phase Objective Key Metrics Dry Cycle Mechanical functionality Ejection force, alignment Soft Tooling Process parameter optimization Fill balance, cooling rate Hard Tooling Final part validation Dimensional accuracy, sink marks Critical Tests:
48-hour continuous run at 120% operational capacity
CMM inspection of critical dimensions (e.g., stacking interface tolerance: ±0.15mm)
6. Advanced Technologies
Industry 4.0 Integration:
IoT-enabled moulds with pressure/temperature feedback for predictive maintenance
AI-driven cycle time optimization
Sustainable Innovations:
Thin-wall designs (1.5–2.0mm walls) reducing material use by 25%
Hybrid moulds with conformal cooling + vapor technology for energy savings
7. Global Manufacturing Hubs
Region | Specialization | Lead Time |
---|---|---|
Taizhou (China) | High-volume standard crates | 45–60 days |
Germany/EU | Precision automotive crates | 90–120 days |
USA | Customized retail solutions | 75–100 days |
8. Case Study: Foldable Crate Mould
Challenge: Produce collapsible crates with <3s folding time and 10,000+ cycle lifespan.
Solution:
Integrated living hinges via overmolding TPE/PP blends
Sliding core mechanism for button-release features
Result: 40% space savings in storage/transport
9. Future Trends
Smart Moulds: Embedded RFID for real-time quality tracking
Additive Manufacturing: 3D-printed conformal cooling inserts reducing lead times by 70%
Circular Economy: Moulds designed for recycled plastics (rPP/rHDPE) with modified flow paths
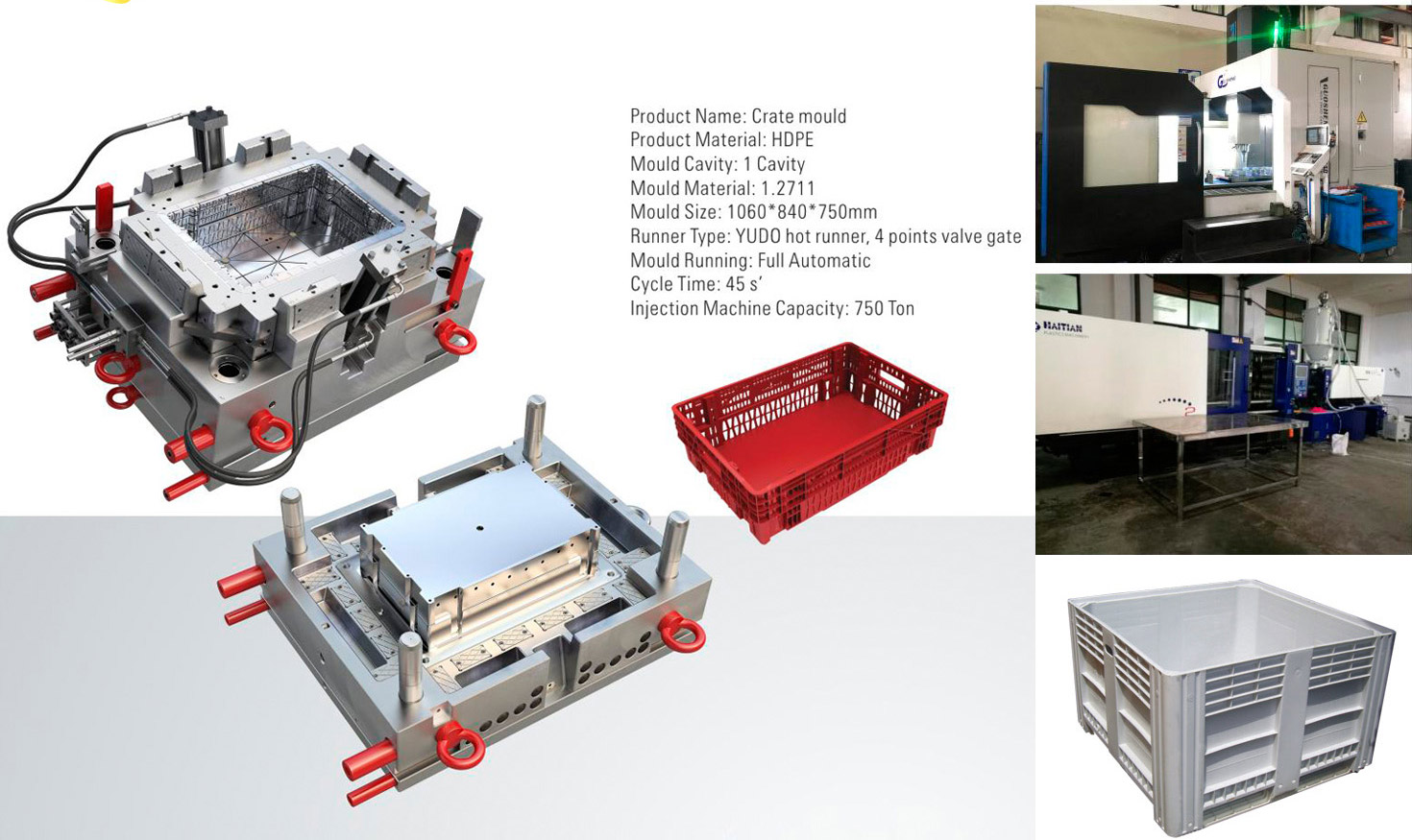
10. Conclusion
Plastic crate mould manufacturing combines precision engineering, material science, and digital innovation to meet evolving industrial demands. Success hinges on:
Rigorous simulation-driven design
Advanced steel processing technologies
IoT-enabled production monitoring
ismmould.com Plastic Injection Molded Crate Mold Manufacturer, Food/Beverage/Folding Plastic Crate Mould
ISM MOULD has a very mature technology for manufacturing plastic crate moulds, the main core steel material of high-quality plastic crate mould is usually beryllium bronze plus DIN 1.2311 steel material. The crate mould runner generally adopts the hot runner way, which can improve the injection efficiency and surface quality of the plastic crate, reduce the injection moulding time of the plastic crates, and avoid the generation of waste when using the cold runner. We adopt the four sides angle pin and slider for taking the side core pulling, then take the stripper plate for demoulding. Plastic crate mould usually use the mould steel such as 45 #, 40Cr, P20, 2738, 2316, 718, NAK80, S136 and so on. It is generally recommended to use 718, P20 materials.
Leave a Reply
Your email address and tel will not be published. Required fields are marked