OEM Big Crate Injection Mould Manufacturing: Revolutionizing Food/Beverage Plastic Crates and Turnover Boxes
The logistics and packaging demands of the food and beverage industry require robust, hygienic, and reusable solutions. OEM big crate injection moulds are pivotal in producing high-performance plastic crates and turnover boxes that meet these needs. This article explores the design, materials, and manufacturing processes behind food-grade plastic crate moulds, alongside key considerations for optimizing cost and efficiency.
1. The Role of Injection Moulding in Food/Beverage Plastic Crate Production
Plastic crates and turnover boxes are indispensable for transporting perishables, beverages, and industrial goods. Injection moulding enables mass production of these containers with precision, durability, and compliance with stringent hygiene standards.
Key Features of Food-Grade Crate Moulds:
Hygienic Design: Smooth surfaces and anti-microbial coatings prevent bacterial growth, complying with FDA and EU 10/2011 regulations.
Structural Integrity: Reinforced ribs and corner supports withstand stacking loads up to 150 kg.
Ventilation & Drainage: Perforated designs ensure airflow for fresh produce and drainage for liquids.
Ergonomic Handles: Molded handles with non-slip textures improve safety during handling.
SEO Keywords: Food-grade plastic crate mould, FDA-compliant crates, hygienic injection moulding, heavy-duty turnover boxes, industrial crate design
2. Design Innovations in Big Crate Injection Moulds
Modern OEM manufacturers leverage advanced technologies to optimize crate functionality and production efficiency:
Critical Design Considerations:
Multi-Cavity Moulds: 4–8 cavity designs boost output by 40%, ideal for high-volume orders (e.g., 10,000+ crates/month).
Interchangeable Inserts: Swap components to produce varying crate sizes (e.g., 20L to 60L) without retooling.
Hot Runner Systems: Reduce material waste by 15% and cycle times by 20% through precise resin flow control.
Nesting & Stackability: Moulds engineered for nested stacking cut storage and shipping costs by 30%.
Case Study: A beverage distributor reduced breakage rates by 60% after switching to crates with glass-reinforced polypropylene (PP) and tapered wall designs.
SEO Keywords: Multi-cavity crate moulds, nestable plastic crates, hot runner systems, custom turnover box design, PP crate moulding
3. Material Selection for Durability and Compliance
The choice of polymer directly impacts crate performance and regulatory compliance:
Material | Advantages | Applications |
---|---|---|
HDPE | Chemical resistance, UV stability | Dairy, chemical storage |
Food-Grade PP | High impact strength, dishwasher-safe | Beverage bottles, meat packaging |
rPET | Eco-friendly, 100% recyclable | Sustainable retail crates |
ABS | Rigidity, glossy finish | Premium-brand turnover boxes |
Pro Tip: Additives like anti-static agents or UV inhibitors extend crate lifespan in harsh environments.
SEO Keywords: HDPE crate moulding, food-grade PP plastic, rPET sustainability, UV-resistant crates, anti-static additives
4. Cost Factors in Crate Mould Manufacturing
Understanding pricing drivers helps businesses balance quality and budget:
Primary Cost Influencers:
Mould Complexity: Intricate features like collapsible sides or RFID tag slots increase machining costs by 20–25%.
Material Volume: Large crates (e.g., 60L) require 3–5 kg of resin per unit, raising material costs.
Tool Steel Grade: Pre-hardened steel (e.g., P20 or NAK80) extends mould lifespan to 1 million+ cycles but raises initial costs.
Certifications: Food-safe compliance (e.g., ISO 22000) adds 10–15% to testing and documentation.
ROI Insight: A $50,000 mould producing 500 crates/day achieves breakeven in 8 months, with <2% defect rates.
SEO Keywords: Crate mould pricing, tool steel grades, ISO 22000 certification, collapsible crate design, ROI analysis
5. Choosing the Right OEM Mould Manufacturer
Partnering with a skilled OEM ensures quality and scalability:
Selection Criteria:
Industry Experience: Prioritize manufacturers with 5+ years in food/beverage crate production.
In-House Capabilities: Look for CAD/CAE design, CNC machining, and full-cycle testing.
Sustainability Practices: Makers offering rPET or bio-based polymer moulds align with ESG goals.
Post-Sale Support: Warranty coverage (e.g., 2 years) and spare part availability minimize downtime.
Red Flag: Avoid suppliers without material traceability documentation or prototyping services.
SEO Keywords: OEM mould manufacturer, CAD/CAE design, bio-based polymers, CNC machining, ESG compliance
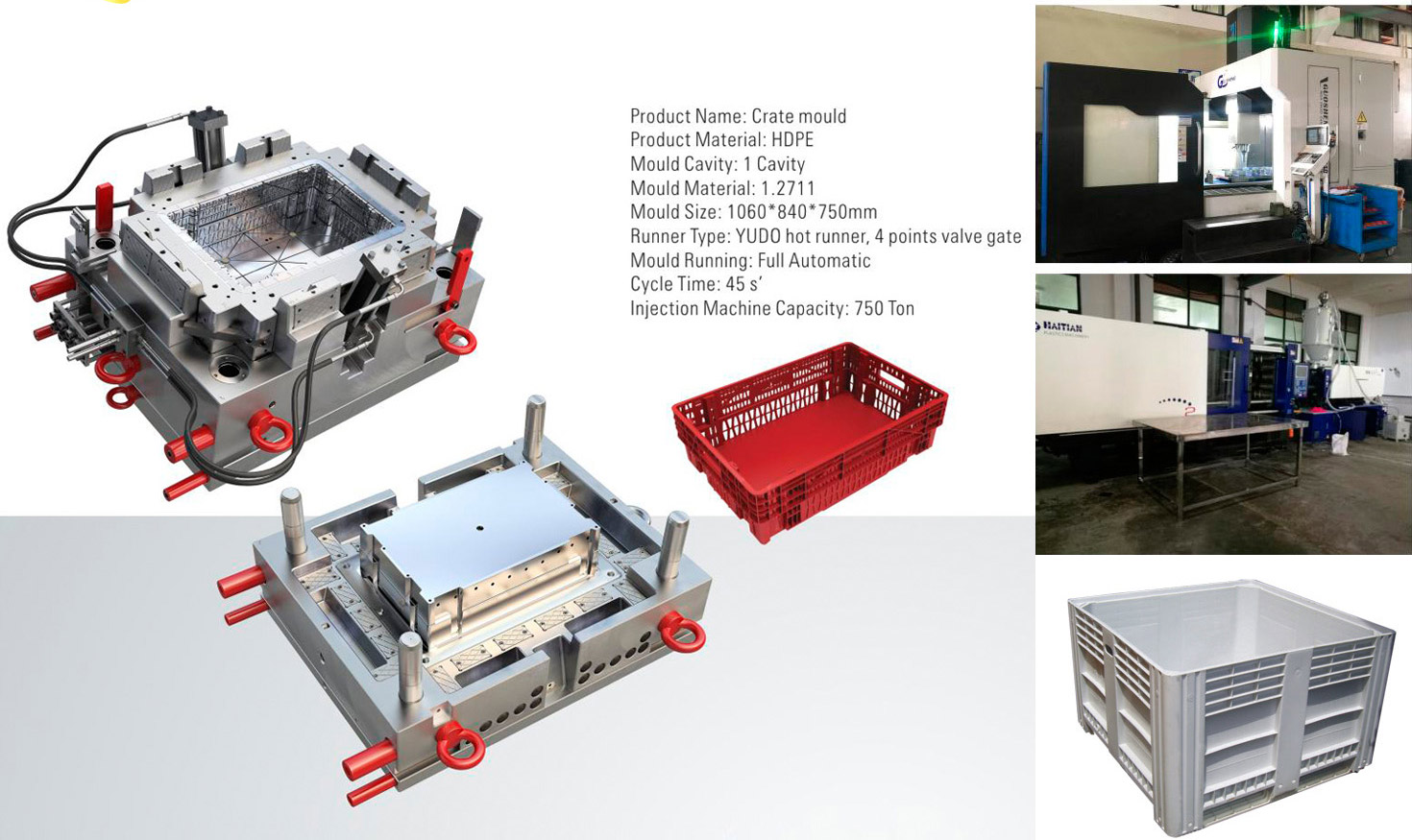
6. Future Trends: Smart Crates and Sustainable Solutions
IoT-Enabled Crates: Embedded sensors track location, temperature, and usage cycles.
Lightweighting: Thinner walls with gas-assisted moulding reduce resin use by 25%.
Closed-Loop Recycling: Moulds designed for 100% recycled content support circular economies.
Conclusion
OEM big crate injection moulds are the backbone of efficient, sustainable logistics in the food and beverage sector. By prioritizing innovative design, compliant materials, and strategic partnerships with OEM manufacturers, businesses can achieve operational excellence while meeting evolving consumer and regulatory demands.
Leave a Reply
Your email address and tel will not be published. Required fields are marked